Why Air Compressor Uptime Matters to Any Business
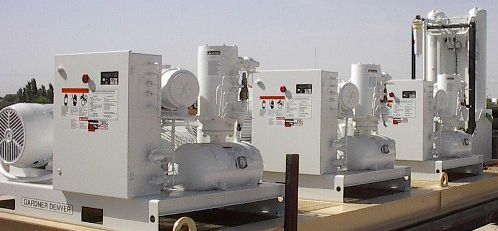
Industrial air compressors require regular inspection and maintenance to prevent costly downtimes and repairs. Many facilities rely on the optimal performance of their air compressor for energy-efficient, safe, and effective production output.
In this blog, we’ll cover the various applications of air compressors in different industries and the best practices to ensure maximized efficiency and uptime for your air compressor.
Essential Functions of Air Compressors in Different Industries
Air compressor systems have many uses and applications across multiple industries. Primarily, air compressors are designed to support heavy-duty operations, especially those requiring non-heat-producing power sources. Here are some of the industries that benefit from and require air compressors for their daily operations.
Construction
Many construction tools and equipment rely on the constant supply of compressed air, such as drills, nail guns, compactors, and jackhammers. In addition, industrial air compressor uptime is critical for construction crews performing lifting operations.
Aerospace
Aerospace component manufacturers require reliable compressors for their daily operations. As a result, they have no room for production errors which lead to significant losses.
Energy
Offshore platforms, oil rigs, and other energy facilities require reliable industrial air compressor uptime. This industry relies on flexible, low-maintenance, and dependable power for a variety of applications such as
- Boilerhouse ventilation
- Powering pneumatic tools and equipment
- Controlling coolant circuit valves
- Operating motion compensators
Pharmaceuticals
Pharmaceutical companies have increasingly relied on air compressor systems to run pneumatic tools for medicine production. They’re vital for shaping, mixing, coating, and hardening tablets and pills.
Food Industry
Finally, food and beverage companies also use air compressors for various operations. For example, they’re essential for food mixing, nitrogen generation, food filling, and packaging.
How To Ensure Industrial Air Compressor Uptime
It is vital to have an experienced and qualified service provider overseeing preventive maintenance to reduce air compressor downtime, which can be costly since it halts production in your facility. Routine maintenance involves various processes, which include the following:
Changing the Oil and Lubricants
Not all air compressors use oil, such as non-lubricated reciprocating compressors that are outfitted with Teflon piston rings. But, with pneumatic devices that do require oil, they have air compressor parts reliant on lubricants that need to be changed regularly.
Metal air compressor parts produce friction and can place stress on your system. In addition, the lack of lubrication can reduce the industrial air compressor uptime since it can’t perform optimally. Oil and lubricants need to be free of impurities and have proper viscosity to circulate correctly. Oil levels also need to be maintained at recommended intervals.
Replacing Air Filters
The air filters in your industrial air compressor gradually accumulate dirt and debris throughout daily use. Clogged filters obstruct the system’s performance and contribute to air compressor downtime.
It forces the system to work harder, exerting more energy to perform basic functions. Not only will it lead to excess energy consumption, but it can also lead to costly maintenance. It’s best to replace the air filters annually or as specified in the compressor’s maintenance guide.
Cleaning Fuel Tanks
If you’re using fuel-powered compressors, their tank will require extra maintenance work. Particulates can accumulate inside the fuel tank. These contaminants can cause various problems such as clogs, component failures, and corrosion. Fuel tanks need to be cleaned annually to ensure industrial air compressor uptime.
Cleaning Intake Valves
The intake valves regulate the internal pressure by opening and closing the air intake of your compressor. Once the required pressure is achieved, your compressor switches to the unload mode, which triggers the unload valve to close almost completely. The system won’t take in more air in this condition, preventing compression and reducing pressure.
An industrial air compressor requires clear intake valves to function at full capacity. After weeks of continuous operations, air-bound elements and dust particles can get sucked into the valves and vents, causing them to clog. This is why it’s recommended to clean the intake valves weekly.
Belt Inspection and Replacement
Compressor belts require proper tension so the entire system can operate efficiently. The belts need to remain flexible yet firm, ensuring the pulleys of different connected parts remain balanced. Through regular wear and tear, rubber belts crack and will require replacement. Without proper maintenance checks, the belt can snap during normal operation. Inspect them weekly and adjust the tension when necessary. Replace the belt when cracks and other signs of wear and tear are observed.
Oil Filter Replacement
Oil filters need to be checked weekly. This process is essential for both lubricated and non-lubricated systems. The filters need to be replaced at required intervals, ranging from 4,000 to 8,000 hours or as needed. If you find the filters heavily coated in oily residue during an inspection, you should replace them as soon as possible.
The residue build-up in the filters can degrade the quality of compressed air passing through the entire system. In addition, it impacts air cleaners, pneumatic spray painters, and other applications where oil can contaminate surfaces.
Ensure Air Compressor Uptimes with Fitz Equipment
Air compressor uptime is vital for many companies for uninterrupted operations. As such, businesses should perform regular maintenance to prevent production loss and avoid costly downtime and repairs. Contact Fitz Equipment today and leverage more than 100 years of combined industry experience to ensure maximized uptime and proper air compressor maintenance.