How to Plan a Successful Air Compressor Maintenance Budget
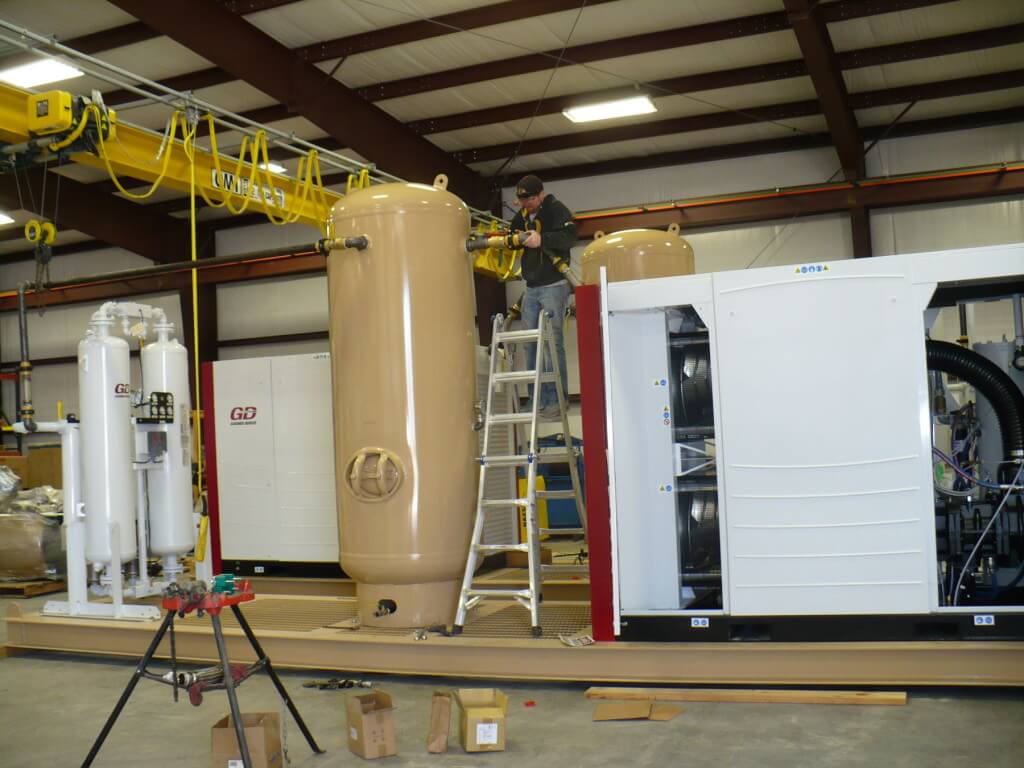
So you’ve done it. After careful planning and financial forecasting, you’ve made a crucial investment for your business by buying an industrial air compressor. Now, we want to let you know that this isn’t where the cost ends. It’s also vital for you to put some time into planning for the various costs associated with operating your air compressor. And one of these often forgotten costs is budgeting for annual maintenance and air compressor repairs.
Like most things in life, if you regularly maintain your expensive or budget air compressors, your maintenance costs shouldn’t be too high. Now maintenance only composes about 5-10% of annual compressor-related expenditures. However, if maintenance is forgotten or deferred, you will see unexpected and expensive downtime. That’s right. Routine checks will help prevent more significant issues later on.
And so what we’re saying is that without a budget for your maintenance costs, any issues such as equipment failures could put a halt to your business’s operations. But with an accurate budget in place, you can experience smooth sailing and extended life of your equipment.
A sound maintenance budget will help ensure your equipment stays in tip-top shape. This post looks at the benefits of creating an air compressor maintenance budget, how to develop an accurate picture of these maintenance costs, and what preventative maintenance looks like.
Benefits of scheduling an air compressor maintenance budget
One of the main benefits of having a maintenance budget is that it generally means setting up a regular maintenance plan. This in itself will help you to prevent significant issues by routinely checking up on your air compressor. No need to wait until something breaks and then face high costs and possible production downtime. Let’s look at the benefits of a maintenance plan:
- Your expensive or inexpensive air compressor and production system will run reliably and at peak performance.
- Your equipment will have a longer shelf life.
- You shouldn’t have to face unplanned downtime in production.
- You can plan for costs and shouldn’t meet large unexpected expenses.
- Your working environment will be safer for your employees.
What determines maintenance costs?
If you’re wondering how exactly you can plan for maintenance costs, we have some tips to consider.
- What compressor do you have? Determining how frequent your service intervals need to be will depend on the type of air compressor you have – if it’s oil-injected or oil-free. If you have an oil-lubricated compressor, you can expect to have more services in the future, as you will need to change the oil.
- Where have you set up your compressor? Where your compressor is housed makes a difference. If you have a harsh environment that is perhaps hot, humid, dusty, or dirty, you’re looking at more regular maintenance.
- Are you only operating cyclically or seasonally? If your working cycle isn’t daily, you can adjust your maintenance period accordingly. But try not to go more than a year between service intervals.
- How often is your compressor being used? There are degrees of usage, but you will have more significant maintenance needs if your compressor is being used extensively. Of course, if you have backup compressors, you can perhaps extend your maintenance plan a bit as you cycle your operating hours between compressors.
- What kind of cooling system do you have? While this is a separate entity to your compressor’s maintenance plan, the type of cooling system will affect your maintenance regime. So, for example, if you have an open cooling tower in an area with a lot of dust or dirt, you may need to clean your compressor more frequently.
Don’t forget about your auxiliary compressor equipment and safety levels. That’s right, your dryers, filters, and drains also need to be serviced, and most likely, more regularly than the compressor. Also, your business’ safety policies will define how regularly your equipment should be examined or repaired, so take careful note of these.
Essential preventative maintenance
Many maintenance tasks can occur at different times throughout your compressor’s life cycle. Here we look at some vital interval checks.
- Daily: Check fluid levels, inspect for leaks, and check the dew point on dryer systems
- Weekly: Clean the compressor, the intercooler’s surfaces, and the air intake filter. This is an excellent time to look for further issues such as leaks.
- Monthly: Inspect the belt tension, clean the fluid cooler fins and aftercooler, and service the air filter.
- Quarterly: Change out the lubricant and check the oil filter.
- Biannually: Change out synthetic lubricant and take fluid samples. Clean the compressor, strainer screen, and crankcase.
- Annually: Lubricate the motors, change out the air/fluid separator, test safety: the valves and the shutdown system are working.
- Biennially: Replace V-belts and check valves if you have a lubricant-free rotary screw compressor.
And so, it’s pretty clear that by budgeting for your compressor’s maintenance plan, you can help improve your company’s operations and save money in the long run. That just makes good business sense.
It’s essential to review and restructure your maintenance budget and plan each year, especially if your working conditions have changed, if you’ve added compressor units or if your production demands have increased. These annual checks also help you find if any of your equipment is underperforming or is perhaps being overworked and how you can update and fix these problems.
For Air Compressors Repair and Maintenance Call the Experts
It’s time to develop an effective maintenance plan. If you are looking for advice on how to do this or what filter is best for your expensive or inexpensive air compressor or even if you’re in the market for new industrial equipment, contact the experts at Fitz Equipment. We have experience and understanding of what will be best for your business. Whether you have a budget air compressor or a top-of-the-range one, we also handle the servicing of air compressors and torque converters.
With over 50 years of dependable, fast, and friendly service, Fitz Equipment manufactures parts for torque converters and specialty machine parts. This family-owned business commits to superior customer service.