Industrial Air Compressor Maintenance Checklist
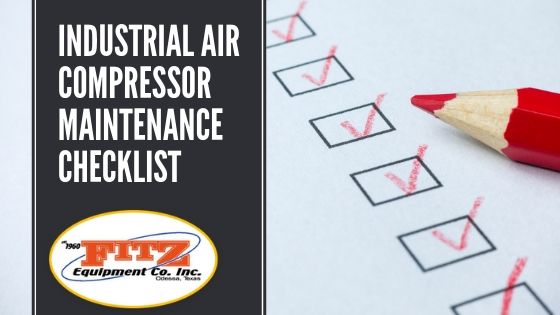
Many industrial processes rely on air compressors, a power tool used for creating and moving pressurized air. Air under pressure has considerable force, making it helpful in powering different kinds of mechanisms. However, industrial air compressors require regular inspection and maintenance like any other machine.
Industrial air compressor repair and preventive maintenance ensure proper operation, helping to avoid downtime, costly maintenance, achieve lower energy costs and extend the life of the device.
This is where a comprehensive air compressor maintenance checklist becomes invaluable. A well-designed guide allows technicians to perform routine inspections, lubrication, cleaning and other necessary tasks appropriately. By following a list, operators can ensure that all essential activities are carried out promptly while minimizing the risk of unexpected failures.
Safety Precautions During Air Compressor Maintenance
Safety precautions are of utmost importance in industrial settings, especially when it comes to industrial air compressor maintenance. So before performing any activities, make sure that the following procedures are implemented:
- Proper shutdown: It is essential to shut down the equipment following the manufacturer’s guidelines. This ensures the compressor is not running and poses no immediate danger during maintenance activities.
- Personal protective equipment (PPE): Appropriate PPE should be worn to protect against various hazards. The specific PPE requirements should be determined based on the dangers associated with the maintenance tasks.
- Adequate training: Adequate training must be provided regarding safety protocols and processes specific to industrial air compressors. Also, regular refresher training sessions should be conducted to reinforce safety knowledge and keep personnel updated on any regulation changes.
What To Check During Industrial Air Compressor Maintenance
Each component plays a vital role in the overall performance and efficiency of the industrial air compressor. So, let’s dive into the specific areas that require attention during maintenance:
Air Filter
It is essential to ensure the air quality from the compressor is optimal before it is used to power various functions. The air filter is crucial in separating impurities before the air leaves the machine. After operating, the component will have impurities, dirt and other particles. Cleaning and changing this part regularly helps to avoid expensive industrial air compression repair.
Inspect for any signs of clogging, dirt buildup or damage. A clogged or dirty air filter can restrict airflow, reducing the compressor’s efficiency and potentially causing overheating. If the filter is dirty, it should be cleaned according to the manufacturer’s guidelines or replaced if it is damaged beyond repair.
Oil Filter
Oil entering the system will compromise the quality of compressed air leaving the machine. Compressed air with degraded quality could end up hurting numerous industrial processes. For example, if the oil filter is clogged or dirty, it can affect the efficiency of the compressor’s lubrication system and may lead to accelerated wear of critical components.
The oil filters should be checked weekly and replaced during maintenance to ensure the efficient running of the machine.
Lubricant
The different internal metal parts and joints are in constant motion whenever the air compressor runs. Lubrication ensures smooth, non-corrosive movement between the metal surfaces that come into contact. By preventing corrosion and tension, the lubricant safeguards against the spread of rust that could erode certain mechanical parts.
During industrial air compressor maintenance, checking the lubricant level and quality is essential. Ensure that the lubricant is at the recommended level specified by the manufacturer. Additionally, assess the condition of the oil by checking for signs of contamination, such as the presence of water, dirt or excessive debris. If it appears to be degraded or contaminated, it should be drained and replaced immediately.
Motor Bearings
Proper lubrication of the motor bearings is critical in ensuring the health and performance of the air compressor motor. These tiny balls rub and roll against each other and the encasement that holds them. Without proper lubrication, rust will form on the surface of the bearings, preventing smooth running. Ultimately, the bearings will become stuck in one place, and the motor will fail.
Regularly inspecting bearings helps to establish whether there is proper lubrication for efficient operation. Look for any wear, excessive play or unusual noise during operation. If there are indications of bearing failure, such as grinding or squeaking sounds, or if the bearings feel loose or rough when rotated, they should be inspected further and replaced if necessary.
Belts
Other important components to check to avoid frequent and costly air compressor repair are the belts. When the rubber belts have proper tension, they are firm and flexible enough to promote balanced movement between pulleys.
However, the rubber is bound to wear down after some time, making it necessary to replace the belts before they lose tension or snap. Industrial air compressor repair would not be complete without inspection and replacement of worn-out belts and ensuring they are in good working condition.
Intake Vents
Industrial air compressors power heavy-duty machinery by transforming air into a powerful force. For this to happen, numerous internal parts work hard to deliver clean, quality air ready to leave the machine. Clean intake vents make work easier for these internal components since not much dirt and dust reach the inside of the device. When dirt particles and grime are in the vents, the machine will have to work harder to deliver quality compressed air.
The intake vents should be inspected and cleaned weekly to keep the air coming in as clean as possible. Inspect the intake vents during maintenance for any signs of blockage or buildup. Clear away any accumulated dirt or debris using compressed air or cleaning tools as the manufacturer recommends.
Check Other Parts
Check several other parts and things to avoid breakdowns and air compressor repair. These include air dryer performance, amps, oil level, temperatures, vibration and voltage.
Create an Industrial Air Compressor Maintenance Plan
Proper and regular air compressor maintenance will go a long way in helping to keep the machine running efficiently and extend its life.
Don’t let maintenance tasks overwhelm your resources and productivity. Contact Fitz Equipment today and let our skilled professionals care for your industrial air compressor maintenance needs. Trust us to keep your equipment running smoothly, minimize downtime and optimize performance, allowing you to focus on your core business operations.
Take the first step towards hassle-free maintenance and schedule an appointment with our team. Contact us now to experience the benefits of professional industrial air compressor maintenance.