How To Stop and Start An Industrial Air Compressor
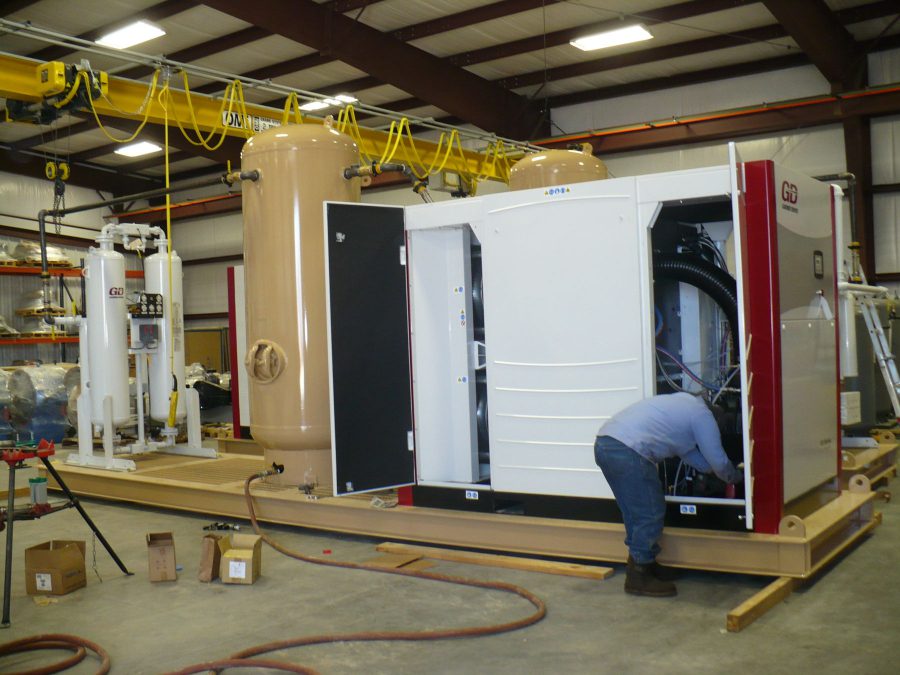
The unique capability of industrial air compressors to operate at higher pressure levels continues to provide reliability and flexibility – making them ideal for many commercial and industrial purposes.
With a CAGR forecast of 3.1% from 2021 to 2026, the USD 14.52 billion industrial air compressor market continues to be the best choice in delivering compressed air for complex industrial processes. However, these compressors do not have to continue running all the time. As such, all operators should have definitive knowledge of the correct way of stopping and starting industrial air compressors.
Production demands shift over time. If you slow down or stop production, you should temporarily shut down your compressed air system as well. Employ the following industrial air compressors best practices to ensure your equipment’s durability and prolong its lifespan.
The Right Approach to Stopping and Starting Industrial Air Compressors
You can leave the air compressors continuously turned on during regular duty cycles. But it is not advisable to keep the compressors running if you will not be using them for an extended duration. During long periods when production comes to a halt, you need to drain and deactivate your air compressors.
How to Stop or Pause Air Compressors Due to Factory Closure or Shutdown
Regardless of whether you integrate the air compressor into a central controller, you need to stop or pause it during production downtime manually. Ignoring this critical procedure may cause your equipment to run at minimal capacity, compensating for any small leaks in the compressed air. As a result, it can harm the machine because it will create unnecessary condensation.
Depending on the equipment type, you need to carry out different procedures. Follow these industrial air compressors best practices to stop or pause your machinery effectively:
- Variable Speed Drive (VSD) Compressors: When executing a program stop for your VSD compressor, make sure to keep the electrical power supply turned on. This step is crucial for having a fully-charged capacitor bank anytime you need to bring it back up.
- Oil-Free Z Air Compressors: After stopping this type of air compressor, you will need to rotate the main drive shaft manually – three complete rotations – at least once a week. You should perform this manual rotation through the motor drive coupling. The purpose of this practice is to stop both low and high-pressure compression stages from seizing up during downtime. Take note that if it has the VSD version for the Z compressor, you need to turn the power supply back on while doing the rotation. This extra step will help protect your machine’s inverter drive capacitors.
- Water-Cooled Air Compressors: When it comes to water-cooled air compressors, you need to isolate the water supply as soon as you stop it. This integral approach will prevent condensate from forming and eventually harming its internal components. In addition, you should also turn off air blast cooling systems.
- Centrifugal or ZH Air Compressors: While the machine is currently off after shutting it down, remember to leave the power supply on for its auxiliary oil pump. Conducting this step will help maintain proper oil temperature during long periods of downtime by circulating warm oil around the bearings via the auxiliary oil pump.
How to Start Industrial Air Compressors After Long Periods of Shutdown
Before turning the machine on again, it is necessary for you to perform a visual inspection first. Consider this as a preliminary step before you conduct the actual switching on of the equipment. You can follow the general guidelines listed below. These guidelines will help you execute the correct process of starting industrial air compressors after being temporarily off for an extended period of time.
- You will need to turn off the power supply connected to the compressor to enable you to inspect its internal components thoroughly.
- Check if the drive coupling can turn freely by removing the shaft protection guard and turning it manually.
- If you can manually rotate it freely, you need to re-fit the shaft protection guard and turn the power supply back on.
- Turn on the air blast cooling system and the cooling water for water-cool air compressors.
- Before turning on the air compressor, make sure to close the air compressor discharge valve.
- Finally, open the air discharge valve slowly until air pressure between the air net and the compressor equalizes.
After the final step, you can now bring the compressor back into operation. Do not forget to ensure that your air compressors are correctly integrated into the controller or optimizer if connected to a sequence controller.
Take the Guesswork Out of Air Compressor Operations
Industrial air compressors are a considerable investment and one of the vital components of any production facility. As such, its operation should never involve guesswork – even if your goal is just to stop or start it. Follow the industrial air compressors’ best practices outlined above to ensure your machine stays in pristine condition, whether during peak production or downtime.
Do you need further assistance with air compressors? Contact us and let our 100 years of combined experience help you with your machinery.